Blog
Different types of machinery used in natural stone processing
Natural stone processing is a complex mechanism and there are hundreds of things that go into processing the stone in a precise and effective way. A granite factory employs a number of machines and other equipment to cut the stone in a specific way. If you are wondering how the stone is processed and what kind of machinery is used for same, continue reading this post to know more.
What is granite manufacturing?
Being a natural stone, granite is extracted from the belly of mother earn in the form of heavy, big-size blocks. As it is very difficult to use these blocks right in a construction project, they need to be processed in different ways to cut it into specific sizes, work on its surface to get a finish, process its edges, and numerous other things. This is where the role of choosing the right granite machinery becomes necessary.
From trade perspective, granite importers and construction contractors always look for granite manufacturers or exporters that have in-house manufacturing capabilities like Regatta Granites India. They have two granite manufacturing units in North and South India that give an amazing granite processing capabilities.
There are different types of machine equipments used in granite manufacturing and its processing. Let’s take a look at them below.
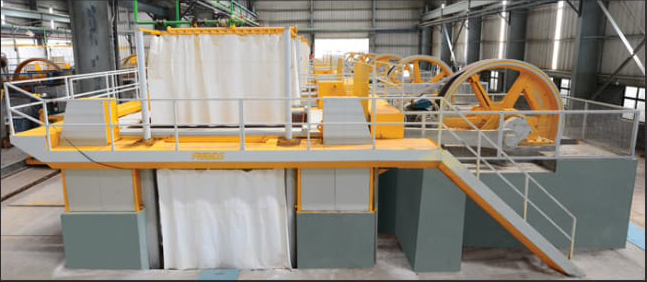
1. Jumbo Granite Gangsaw
As its name indicates, this machine is mainly used to but huge granite blocks into gangsaw slabs. It is a heavy machine that comes at a high price and complex installation. The granite blocks are put on a platform and then it glides under the blade which runs at a higher speed to cut the blocks into gangaw slabs. This is what gives this machine its name.
This machine is also known as a diamond row saw, diamond frame saw, and granite frame saw. The saw frame can be assembled with 60/80100/120 diamond saw blades. A jumbo granite gangsaw yield high straightness, better cutting quality and improved output.
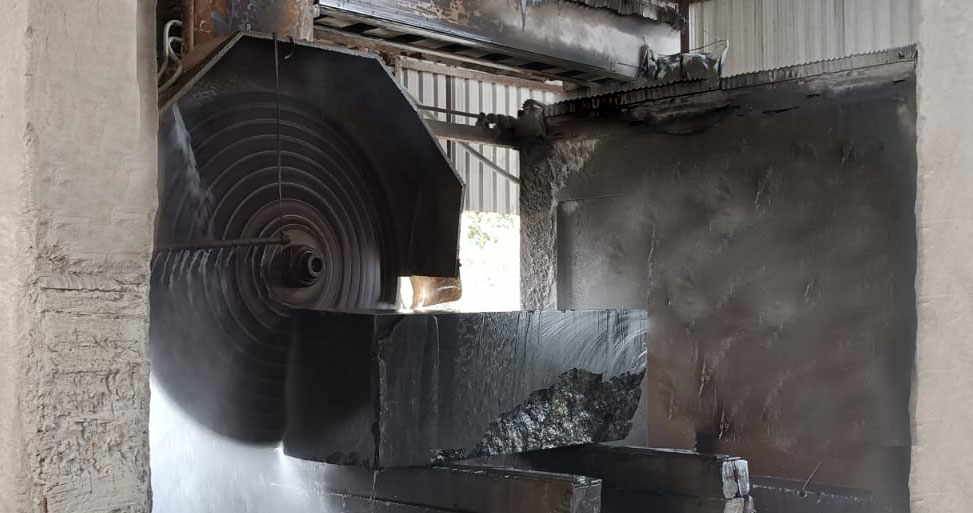
2. Multi Block Cutter
With up to nine diamond circular saw blades, a multi-blade block cutter can cut a variety of stone blocks into slabs of different thicknesses. Some machines have a basic, functional design with a robust steel and cast iron construction that ensures maximum stability and extreme precision during sawing.
In addition, the machine’s running route is guided by linear motion. Ball screw for quick up/down mechanism, to guarantee optimal anti-rust protection. When compared to a standard machine of the same type, a lubricant system can significantly lower maintenance costs and frequency, resulting in a precisely cut machine.
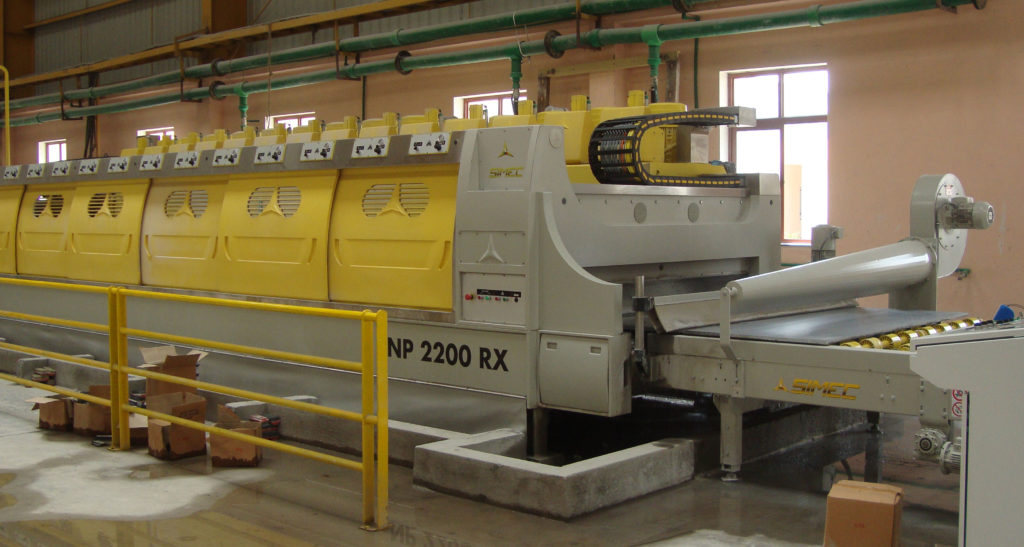
3. Automatic Slab Polishers
An automatic slab polisher is intended to apply polish on the surface of the stone slab. This machine carries a platform on which the slabs are placed evenly. A polishing arm skids over the surface and applies polish all over the surface. Today, the quick adoption of newer technologies allows for free movement of spindles in order to help optimizes the total area utilized on each granite slab. The eventual outcomes help granite exporters save costs through automation and level up the revenue produced with each slab being used to its optimum capacity.
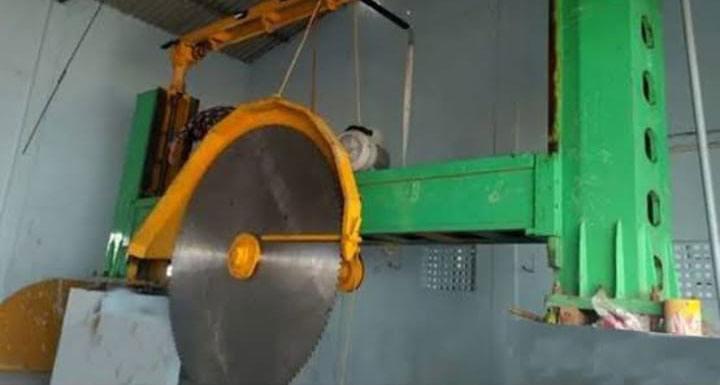
4. Single Blade Block Cutter
This type of cutting machine employs a single blade to cut the block. The functioning of this machine is quite similar to that of multi block cutter and the only difference lies in the no. of blades. Since cutting a block involves a lot of time, using one blade for cutting increases it manifold.
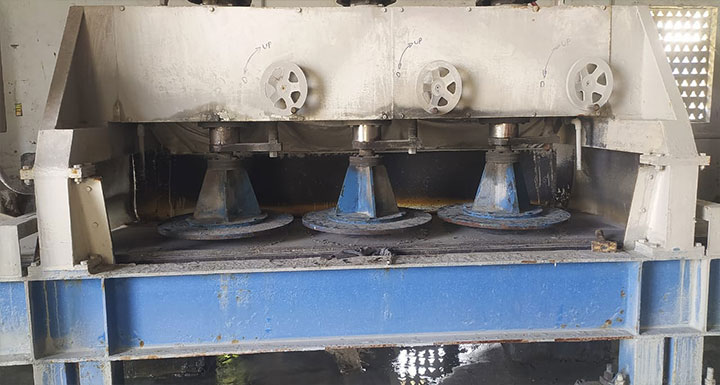
5. Calibration Machine
A stone calibration is used by granite and granite exporters to calibrate the stone in the most effective way. Most of these machines come with custom-designed spindles and calibrating heads that work automatically.
When the size of the granite tile changes, the machine can accurately calibrate all granite tile sizes and doesn’t need the diamond tools to be changed. The machine comes in different sizes working usable width available.
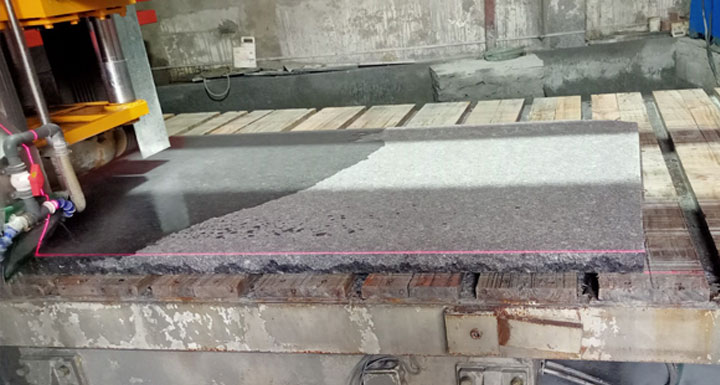
6. Bridge Cutter
A bridge cutter machine is used in the natural stone industry to process granite countertops and other stone products. This machine allows granite manufacturers to cut granite slabs into any size and shape they need.
The saw comes with a water-cooled diamond blade that keeps the granite from chipping or splitting. Lastly, the stonemasons shape the ornamental edge Annie desires for her countertop using handheld tools for polishing and grinding.
The Conclusion
The role of choosing the right granite manufacturing machines is very important as precision plays a pivotal role in making an effective use of granite across diverse applications. Our dominance in the sector is demonstrated by the sophisticated equipment we use to manufacture granite. We at Regatta Granites India are prepared to provide our clients with the best granite slabs, tiles, and other items, from cutting large granite blocks to meticulously processing granite tiles. This is one area in which we significantly outperform our rivals.