Blog
Life cycle assessment of granite stone
Whenever it comes to determining the most widely used materials for construction, granite always finds a place in the list. For ages, granite has been used in the construction industry. And the most remarkable thing about this natural stone is its hardness, longevity, and design that entices onlookers like nothing else.
Being a widely used construction stone, granite comes in a wide range of colors and patterns. Here is a post that puts light on Granite quarrying and process from a life-cycle inventory (LCI) perspective. This analysis is done by The Natural Stone Council in association with various businesses, trade associations, and natural stone suppliers.
What is Granite?
Granite is termed an invasive igneous rock which is immensely disseminated all across the Earth’s shell at a band of depths up to 31 mi (50 km). Granite’s typical grainy composition and strength is the outcome of various separate crystalline assemblies which hold tightly together as magma gradually cools within large, profoundly suppressed rock bodies called plutons. True granite tends to have 20-70% quartz along with plagioclase and base feldspars of which the earlier may not go beyond the usual balance. Other crystals like biotite may also appear in granite, considering its diversity of entrances.
On the commercial front, Granite refers to a variety of other kinds of non-granite dimension stone such as feldspathic crystal-like rocks or other eruptive or metamorphous rocks which have similar qualities to granite’s gritty, interlacing texture. Several variations of granite emerge on the commercial market with white, black, pink, grey, and red being the most widely found hues. Greens and browns are also available along with shadier grays and black.
Granite Quarrying


Also known as extraction, the granite quarrying process is comprised of eliminating blocks or parts of stone from a recognized and exhumed geologic deposit. Variations in the specific quarrying techniques used sometimes emerge from differences in the physical properties of the deposit itself like density, fracturing/bedding planes, and complexity—financial thoughts, and the site owner’s penchant. Nonetheless, the process is comparatively easy: find or develop (negligible) breaks in the stone, wipe out the stone employing heavy machinery, place the stone on a vehicle for transportation, and shift the material to storage and further use by a granite supplier. Please refer to the below diagram that highlights the quarrying operation.
According to the diagram, the initial step is to get access to the granite mine. This is done by eliminating the initial layer of the earth and rock inappropriate for use typically referred to as overburden. Once the appearance of the granite gets revealed, the stone is extracted from the quarry in benches, generally 8 to 12 feet square spreading 20 feet or more using various techniques suitable to the geology and features of the granite buildup.
The quarrying process includes the hole drilling along the bay perimeter, shadowed by either cutting the stone out of the deposit using saws loaded with diamond wire or by excruciating the stone employing heavy hydraulic splitters or low-range explosives. After the seat is cut or split moveable from the deposit, heavy equipment is utilized to raise the granite bench and move it to an examination bay for grading, temporary storing, next-stage preprocessing into slabs, and ultimate shipment from the quarry. Granite of deficient quality or dimension for the raised demand is stored on-site for further usage, crushed for utilization in paving and construction applications, or stored for other site recovery doings.
Granite Processing
Granite Processing activities include a higher level of variation as compared to extraction. However, the usual procedure starts with primary cutting, followed by finishing the stone, and sum up with a second cutting or shaping. Due to the variety of stone products, the second and/or third steps may be scrapped, precisely when the product possesses a “natural” appearance. Refer to the below diagram for more details.
The processing of granite starts with the transportation of the rough granite block from the quarry to the processing unit. It should be kept in mind that this step may be inclusive of different transportation steps; before reaching the facility, the stone may be transported to different vendors or distribution locations globally. In addition, some stone blocks may need to be cut into slabs before moving to the primary fabrication plant. These are most commonly cut to a thickness of 3/4 in (2 cm) or 1-1/4 in (3 cm) in lengths of roughly-12 ft and widths nearly 3-5 ft. The path that the stone adopts through the unit thus depends on its physical state upon influx, as well as the product to be made.

The first stage of the process is cutting or shaping the stone. This is usually done using a circular blade saw, but a diamond wire saw, a steel shot gang saw, or a splitter can also be used for this process. When running a circular or diamond wire cutter, an incessant stream of water over the saw is put to reduce the heat generated by the process; the adequately-raised temperature can lead to major machine and material injury.
Different types of finishes can be applied to the granite stone using different tools and techniques. Polished or honed finishing is often applied to granite products, but the use of thermal finishes is also popular. The former is done both manually or mechanically using polishing pads, while thermal finishes are done through a flame.
A secondary shaping step may be required if the product has any features or custom size or shape. Similar to primary cutting, a circular blade saw as well as a diamond wire saw are the most widely used tools for stone processing. A CNC machine, high-pressure water, or a splitter may also be used for shaping job. The water is again used for massive spherical and diamond wire cutters, as well as for cutting with high-pressure water and a CNC. Splitters are usually guillotine-shaped machines that are based on hydraulics.
Once finishing is done, the product is packed and shipped to the storage facility and then sent to natural stone suppliers in different parts of the world. Additionally, it is processed into smaller sizes given the exact requirement of a construction project.
Life cycle Inventory of Granite during its quarrying and processing
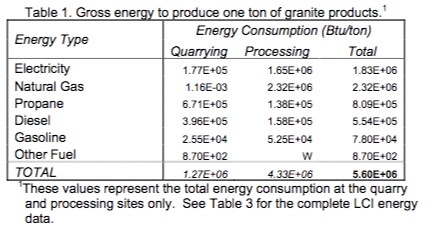
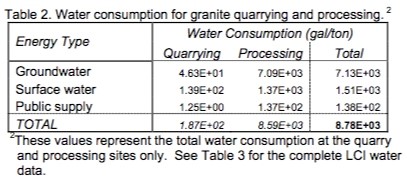
LCI Data Set Quality
The dataset showcased in this analysis signifies nearly 700,000 tons of quarried granite and almost 175,000 tons of dimensional granite products. Data also replicates a variety of operations with regard to size and location. The respondents directed annual quarry production extending from roughly 400 tons to 240,000 tons, while processors stated a range of approximately 90-55,000 tons/year.
LCI Results
Here are the results obtained from the quarrying and processing of granite stones. The average gross energy needed to generate 1 ton of dimensional granite is 5.60 million BTUs. Table 1 reflects the breakdown of this gross energy per ton of granite stone produced. Table 2 shows the water needed for a similar level of production.