Blog
Fully-fledged Granite Factory in India to Process Granite Products
The use of granite in different facets of construction has increased significantly. The reasons are quite obvious – more varieties, better durability, stain and scratch resistance, vivid colors, etc. Be it residential construction or commercial construction, granite emerges as the best choice for architects and construction companies today.
Now, when it comes to importing the finest quality granite, there are several granite manufacturers in India that produce and export the best quality Indian granite in diverse colors and finishes. Most granite manufacturers in India have a dedicated manufacturing unit or granite factory which enables them to process the granite blocks in different ways to get the desired product from tiles to gangsaw slabs, cutter slabs, monuments, countertops, fountains, window sills, steps & treads, RIM stone, etc.
People buy polished, perfectly-edged granite products like tiles, slabs, and countertops for domestic and commercial construction purposes. First of all, granite is extracted from granite quarries in the form of rough blocks of different sizes. End consumers never buy this sort of stone products for construction projects. They prefer to get fit-for-use stone products. That is why a fully-fledged granite factory makes a big difference. A fully-operational factory produces quality granite products matching the exact needs of both B2B and B2C buyers. Find here more about the operational activities of a granite factory regarding granite products produced here.

Zero-defect products from Indian granite factories
With a fully-functional granite factory in India, it is easy to avail final granite slabs, tiles, countertops, vanity tops, monumental stone, and other stone article types. It is a granite processing factory where a rough block takes a unique shape. Be it a white granite or a black granite factory, every stone processing unit is vital for giving rough stones a new form and shape with an assurance of zero-defects. Being lots of granite quarries in India, granite suppliers have established granite factories near quarries and ports.
A certified factory of granite promises zero-defect granite products. In these operational units, granite is produced as per the changing needs of buyers. There are a few processes that all granite factories have to follow to offer the most appropriate and quality construction material. These processes include:
Granite calibrating, cutting, honing, finishing & tumbling
When a stone passes through all these processes, it takes shape of a functional slab and tile. All these processes are accomplished with modern tools.
Granite protection during stone packing, loading, and unloading
All finished granite stone products need proper handling. That is why granite factories use wooden crates, corrugated boxes, and waterproof plastic to protect packed granite products from damage in transit, like chipping and scratches.
Quality inspection of granite stone
No stone product reaches consumers until it is passed through a rigorous quality check. Quality inspectors at granite factories ensure that every slab goes through a regular inspection, rigorous check, and strict monitoring process as per international standards.
Granite stone delivery
This process is concerned with the transportation of granite products from the factory to shipping ports. It is vital for ensuring the safe and secure delivery of packed granite products. It also involves adherence to documentation and shipping procedure.


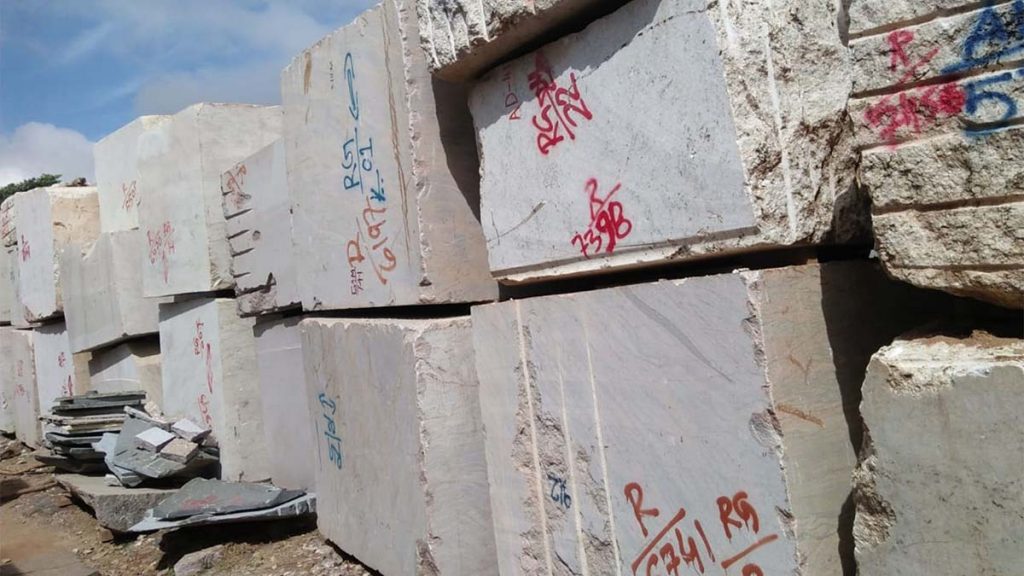
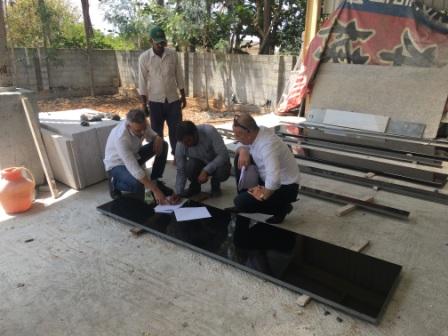
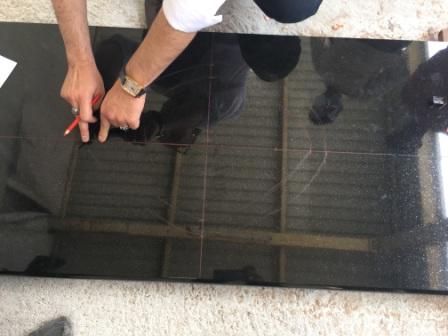
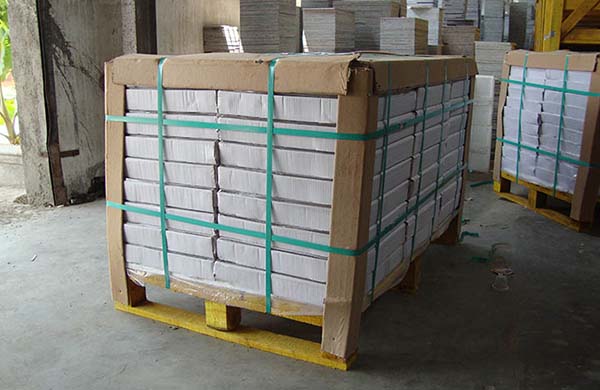
Granite products made at a granite factory
Generally, granite blocks are brought to a granite factory in India in the form of gangsaw and cutter blocks. Primarily, there are two sizes of blocks quarried from granite quarries in India.
• Gangsaw Block Size: 260x160x100 cm up 280x180x100 and 300x190x120 cm up 300x200x100
• Cutter Block Size: 180x70x60 cm up 240x70x60 – 300-320 x 130-165 x 160-205cm and weight 23-29 tons
When a rough granite block enters a granite factory, it takes a definite form and size through various phases. In India, different granite factories produce white, black, red, blue, green, yellow, and grey stone products. B2B buyers can expect the following granite stone types from a factory that processes granite stone in Bangalore or Chennai in India. These include:
• Granite tiles – 30×30, 30×60, and 60×60 cm
• Granite countertops – Custom and standard sizes
• Granite vanity tops – Custom and standard sizes
• Granite color options – White, black, red, green, brown, golden, grey, and pink
• Granite finishes – Polished, lepatora, honed, flamed, bush-hammered, brushed, and leather
• Granite cutter slabs – 180 x 60 cm up in 2 & 3 cm
• Granite gangsaw slabs – 260 x 160 cm up in 2 & 3 cm
• Granite monuments – Custom sizes
• Granite edge finishes – Machine-cut
If you are searching for a granite factory in Karnataka or a granite factory in Tamil Nadu, always contact an ISO-certified granite processing unit in India. Such a factory always produces high-quality products as per global granite production standards.
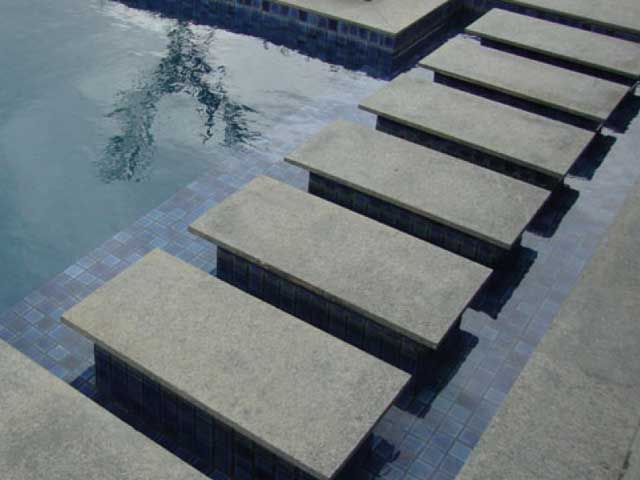
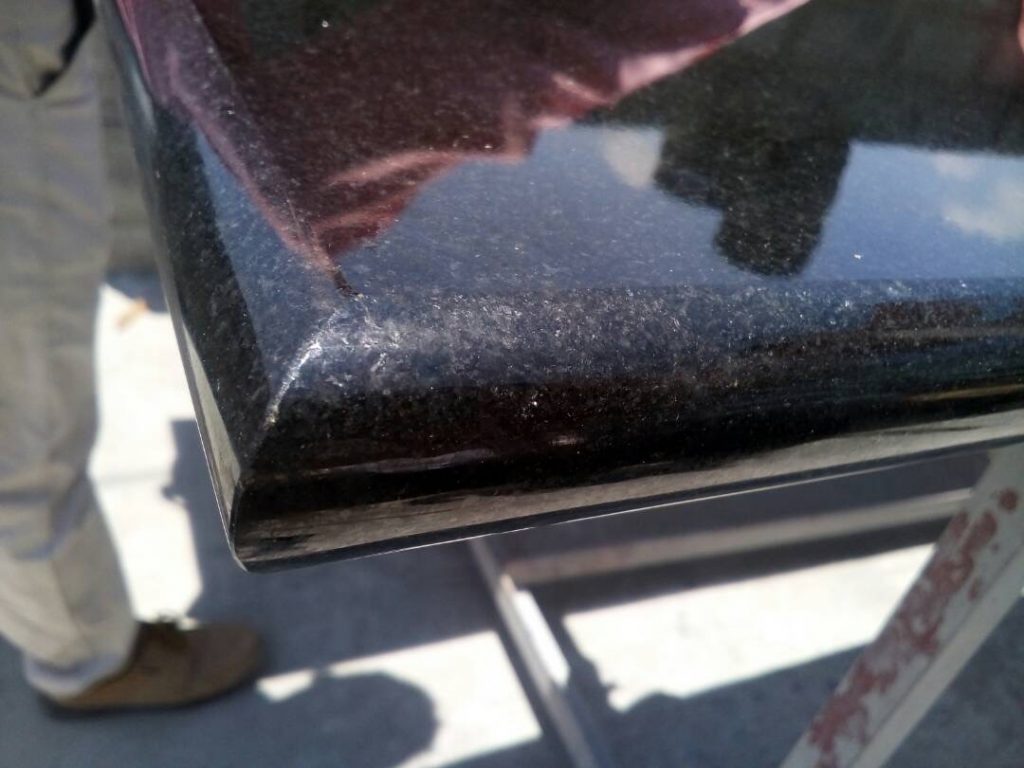

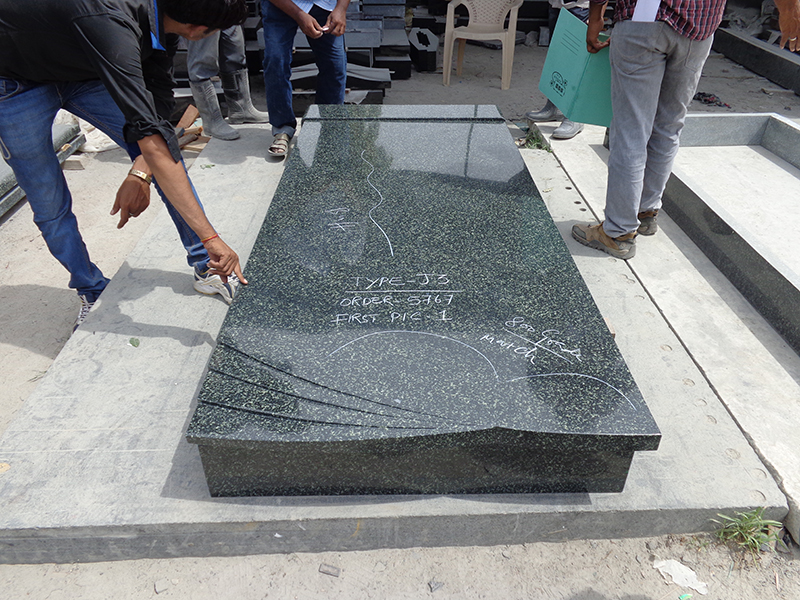
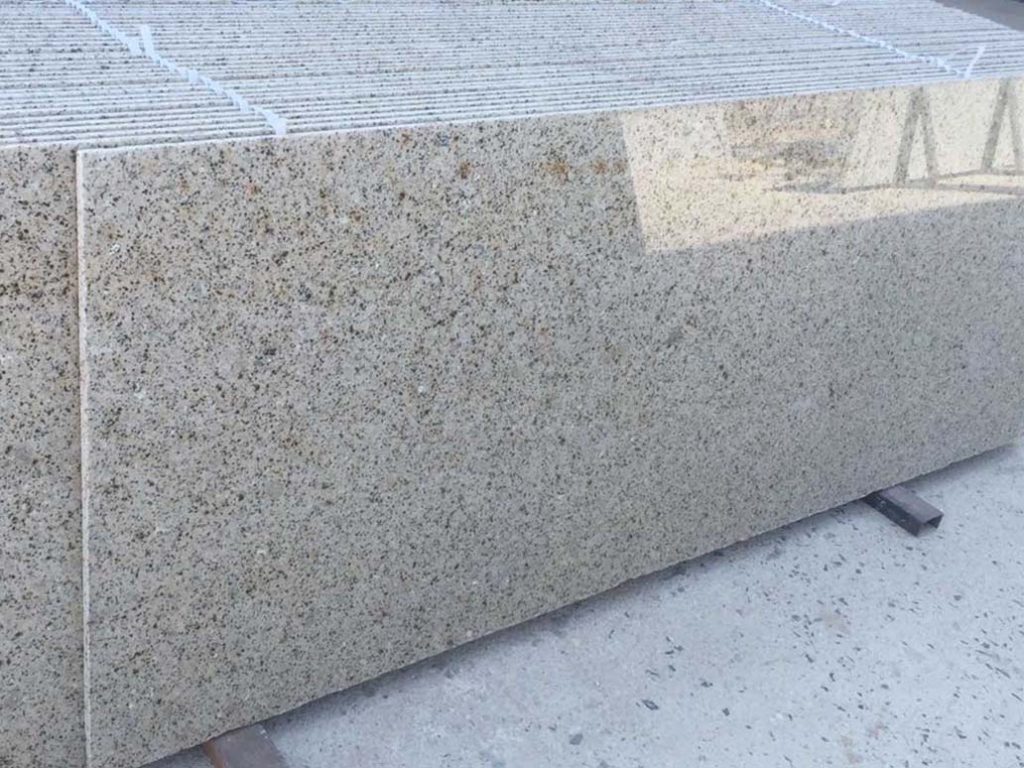
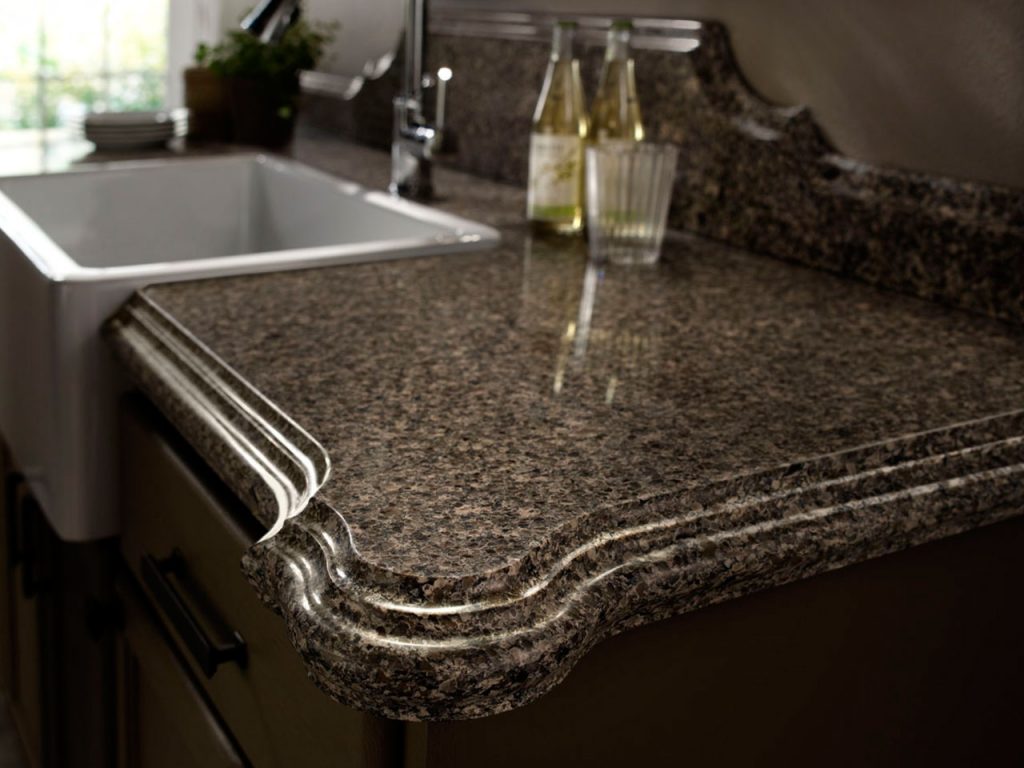
Summing up
It is clear now that a granite factory matters the most when it comes to getting top-quality granite slabs or tiles. B2B buyers interested in buying granite products in bulk can also make a factory visit. It will help them check every process and quality output.
A factory having modern stone cutting, stone polishing, stone edging, and stone shaping equipment can do wonders for B2B buyers.